Safety, Health and Environment Management System
Safety, Health and Environment management system SHE
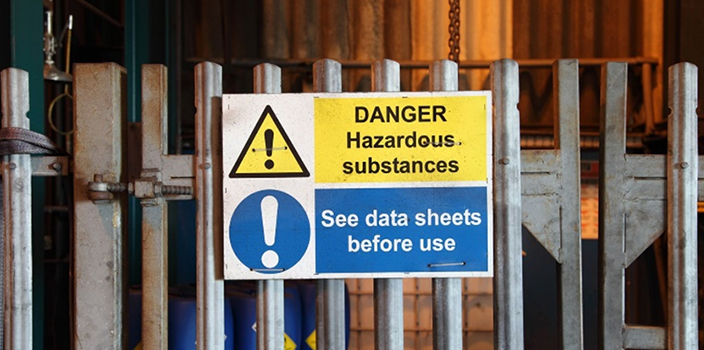
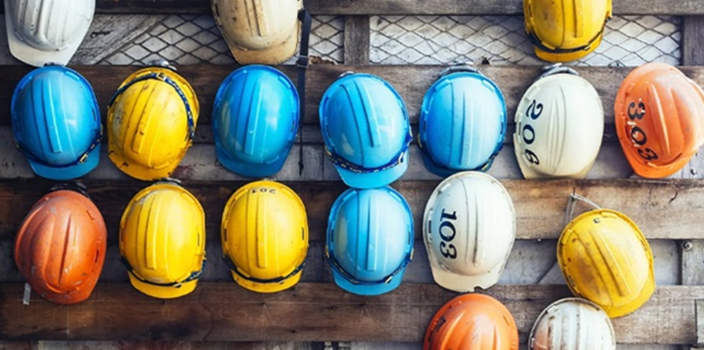
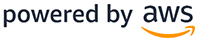
SHE system aims to secure information infrastructure, simplify safety/health/environment-related tasks by innovating processes
and by connecting key systems that share real-time information,
respond to Serious Accident Punishment Act, and to improve task standardization and efficiency.
It maximizes user convenience by statistical management of various data, generating reports, and status check through maps,
and supports a real-time decision-making system by providing summary data on SHE KPI on the management screen.
Importance
-
01
Reinforced legal standards
Increased management costs due to reinforced legal standards such as the Serious Acts Punishment Acts and increased levels of punishment
Increased demands for social compensation and rising levels of corporate responsibility for accidents
Strengthened social and ethical standards/roles for corporations
-
02
Reinforced process
Systematic management of inspection and licensing management activities
Establishment of an integrated disaster prevention monitoring and response system
Maximized efficiency by connecting unit tasks
-
03
Support DX transition of safety, health and environment
Standardization and systemization of safety, health, and environment work
Effective risk management through statistics and history management
Detailed
functions
SHE integrated information
Key functions
It consists of 15 modules and over 300 screens.
SHE business management |
---|
Zero hazard management |
SHE budget management |
SHE goal management |
SHE goal management |
Licensing status |
Laws/Regulations |
My schedule management |
Bulletin board |
Reference room |
Worker opinion management |
Regular report material management for Serious Accident Punishment Act |
Serious Accident Punishment Act dashboard |
Construction/Work permit form |
Construction status |
Daily work permit form |
Safety management |
Safety observation |
Internal accident management |
Emergency response training management |
Near Miss management |
Accident count |
Inspection |
---|
Safety inspection |
Walk-around inspection |
Walk-around inspection |
Facility inspection |
Inspection before operation |
Hazardous machinery and equipment |
Safety and health law implementation inspection management |
Major civil disaster inspection and management |
Government corrective action request |
Process safety data |
List of hazardous/dangerous substances |
Process facility information |
Process chart information |
Building equipment layout |
Explosion hazard area |
Safety design manufacturing and installation |
Self-audit |
Plan |
Result |
Analysis |
Audit scope |
Auditor management |
Change management |
---|
Change management |
Hazard evaluation |
Work hazard evaluation management |
Process hazard evaluation management |
Improvement management |
Improvement requests |
Improvement actions |
Improvement action performance |
SHE education management |
Education plan management |
Education result management |
Education result status |
Education result status |
Education status by person |
Upcoming education status by person |
Upcoming education date by person |
Health |
Checkup |
Health Management Center |
Work environment measurement |
Musculoskeletal system |
Protective gear management |
Environment |
---|
Air |
Water quality |
Waste |
Waste |
Environmental effect evaluation(Life cycle) |
Environmental effect evaluation |
TMS |
Chemical substance |
Status of materials by regulatory item |
Regulation status by chemical substance |
Chemical materials |
Preview |
Chemical materials by department process |
MSDS |
Sample management |
Licensing status |
Management tips for process materials |
Partner management |
Partner management |
Partner evaluation and |
Response to
Serious
Accident
Punishment
Act
With the recent strengthening of the Serious Accident Punishment Act, the need to establish a comprehensive compliance response system is emerging.
WeZON's Serious Accident Punishment Act response module manages the management items required by the Act through a system to support
the smooth process of compliance with legal obligations, CSEO reporting, and government affairs.
Serious Accident Punishment Act overview
-
01
Target for punishment and details
Business owners, responsible managing officers, etc.
Death : At least one year of imprisonment,
or a fine not exceeding one billion wonInjury or illness : Imprisonment for seven years or less,
or a fine not exceeding 100 million wonCorporation or institution
Death : Fine not exceeding 5 billion won
Injury or illness: Fine not exceeding one billion won
-
02
Compensation for damage
If a business owner or a responsible managing officer, etc. violates the duty to secure safety and health intentionally or by gross negligence which result in a serious accident, they shall be liable for damages within the limit not exceeding five times the amount of such damage
-
03
Application scope
Business owners or responsible managing officers, etc. of businesses( business location) with five or more full-time employees
-
04
Enforcement period
Business with 50 or more full-time employees: 1 year after promulgation(Jan 27, 2022)
Business with less than 50 full-time employees: 1 year after promulgation(Jan 27, 2024)
-
05
Related regulations
Enforcement Decree Article 4, Establishment of the safety
and health management system and implementation measuresThe Act Article 5, Duties of business owners and responsible
managing officers to secure safety and healthEnforcement Decree Article 5, Management measures required
for the mandatory execution safety and health related laws
Functions for responding Serious Accident Prevention Act
SHE goal management
Safety and health laws
Execution review management
Work hazard evaluation management
Process hazard evaluation management
SHE education management
SHE budget management
Internal accident management
Evaluation management of
legally appointed persons
Improvement management
Management of appointment/dismissal of
legally appointed persons
Management of inspection
for the implementation of government and local government’s corrective actions
Worker opinion management
Major civil disaster inspection
and management
Emergency response training management
Regular report material management for Serious
Accident Punishment Act
Partner evaluation and safety
and health cost management
Serious Accident Punishment
Act dashboard
Expectations
-
Comprehensive compliance response
Comprehensive compliance response to
Serious Accident Punishment Act -
Provision of PSM response system
Provision of external PSM imprisonment
response system -
Reduced accident occurrence
Reduced accident occurrence
-
Response to chemical regulations
Response to domestic and international chemical regulations by syncing it to the chemical regulation DB
-
Establishment of response system
Establishment of quick SHE decision-making
and early response system -
Enhanced effect of safety education
Enhanced effect of safety education through the management of education completion status
-
Sustainable growth value
Improved corporate sustainable growth value by measuring ESG performance
-
Improved employee satisfaction
Improved employee satisfaction through access to personal health information and follow-up management of those diagnosed with medical conditions
-
Model and process application
ISO45001(Safety & Health Management System)
model and process application
Product and technology inquiry
02-555-7033
info@wezon.com
Integrated Environmental Management System
Integrated Environment Management System iEMS
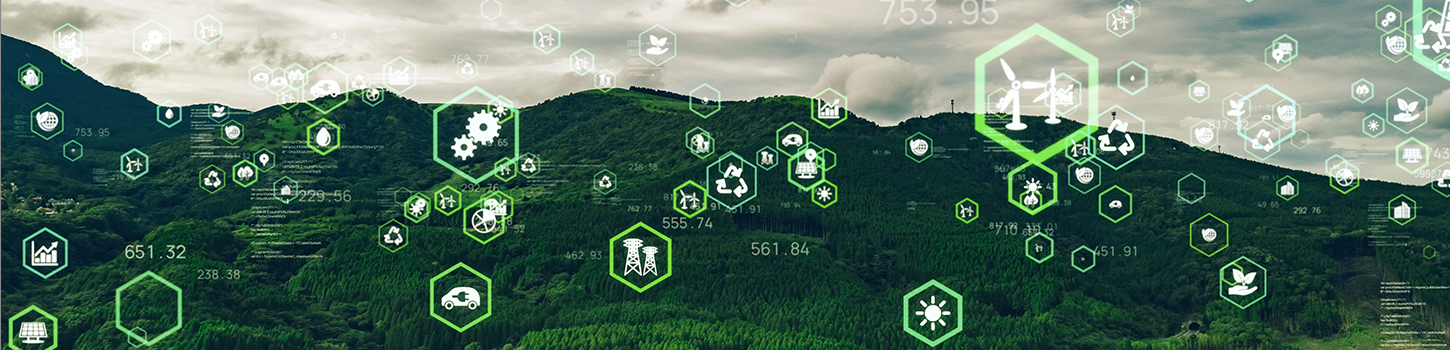

Integrated environmental permits require post-Environmental Management from the time of acquisition,
and re-permission is needed after 5-8 years depending on
the Environmental Management level.
The Integrated Environmental Management System supports smooth re-permission and data management through the integrated
management of environment-related information, including both the information managed in the system and offline.
Through post-management consulting, monitoring and post-environment management become feasible without increased work load, thereby improving work efficiency.
The integrated management workplace is subject to regular and frequent access and inspection(regular inspection and on-demand inspection),
and if you wish to change(or have changed)
important matters among the permitted matters, you must obtain change permit or make a change report.
Since the change permit and change report requirements are divided into pre and post change, it is essential to preview environmental permits in advance if there is an establishment,
expansion, replacement or changes in discharging facilities, or if fuel, raw materials, secondary materials, manufacturing processes, etc. are changed.
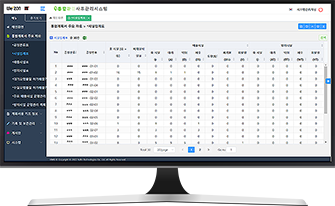
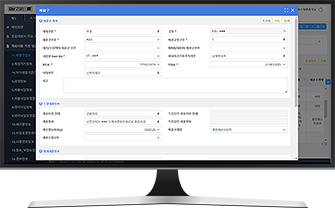
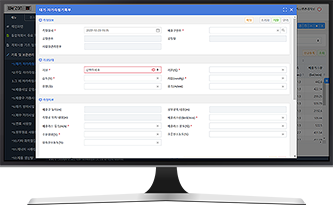
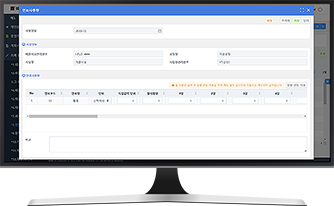
Importance
-
01
A company specialized in environmental safety IT system development
A specialized company that has been developing environmental safety IT systems for 20 years
Establish integrated safety environment management solutions such as SHE system and safety environment portal
Establish specialized systems such as Chemical Management System(CMS), LDAR(HAPs), and PSM portal
※ Establish system that compiles the expertise knowledge(Develop and build system based on the environmental module among SHE)
-
02
Possesses proven performance in various integrated environment licensing
Performed numerous integrated environmental licensing in the organic chemical industry
Completed integrated approval for Hanwha Solutions, Hanwha Impact, BASF Korea, Kukdo Chemical,
etc.(Change permission/reporting after approval also performed)A large number of environmental licensing experts and PM-level personnel who have completed integrated permits
※ Strengthened synergy from integrated environment licensing experience(Integrated environment licensing personnel participate as consultants)
-
03
Sufficient understanding of the customer’s IT systems
Sufficient understanding of the customer’s IT systems(Environmental safety)
Early-stage environmental safety systems(CheMiR, P-HAPS, etc.), safety environment portal, PSM portal, etc.
Smooth cooperation made possible during Legacy I/F based on our manpower experienced in customer's IT system operation
※ Efficiency through understanding the customer’s IT system(Data source identification and Legacy I/F work efficiency)
-
04
Shortened construction schedule due to package-based solutions
Holds integrated environmental(IEMS) package solution
Package solutions are developed in advance, and program registration is complete
Commenced system construction for other business sites(in preparation)
Yeosu B Company, Ulsan S Company, etc.
System scheduled to open in 2023 1H※ Holds package solution and expects to pilot it on another site(Shortened establishment period by reflecting the results of similar businesses)
Process
Key functions
Announcements |
---|
Announcements |
Bulletin board |
Integrated environmental permit management |
Integrated permit history management |
Permit review results report |
Integrated Environment Management plan |
Upload excel file |
Attachments and annex |
Record and preservation history management |
Record and preservation history management |
Upload excel file |
External API |
API for measurement data collection |
API for connecting to other systems |
Record and preservation management |
---|
Air - Self-measurement record |
Water quality - Self-measurement record |
Other self-management records |
Discharging facility operation details |
Outlet operation time |
Air pollution prevention facility operation status |
Wastewater treatment facility operation status |
Fuel usage |
Amount of raw and supplementary materials used |
Amount of other chemicals used |
Energy usage |
Production volume |
(TMS operation status |
Record of other individual law implementation) |
Execution of permit conditions |
Monitoring maintenance management |
Environmental pollution accident prevention and measures |
Key materials from integrated plan |
---|
Process classification table |
Facility count table |
Discharging facility table |
Prevention facility table |
Air pollutant emission standards(Draft) |
Water pollutant emission standards(Draft) |
Operational management plan for key discharge facilities |
Operational management plan |
System |
Common code management |
Menu management |
Authority management |
User/Department management |
Attachment file setting |
Bulletin board management |
Menu management |
Log management |
Basic information |
---|
Outlet information |
Measurement device information |
Permitted discharge standard |
Process information |
Discharging facility information |
Discharging facility pollutant information |
Prevention facility information |
Prevention facility pollutant information |
Waste information |
Non-point source pollution management information |
Fuel information |
Raw and supplementary material information |
Water information |
Other chemicals information |
Energy information |
Production plan |
Discharging monitoring plan |
Device management plan |
Expectations
-
Compliance
Maximize the re-permission period by improving the Environmental Management level through post-Environmental Management using IT(5 years → 8 years)
-
Zero Emission
Improved Environmental Management level, including pollutant reduction through integrated management
of environment-related data -
ESG Management
Establish a foundation for integrated performance management in the “E”(Environmental) area,
the most important axis of ESG management
Product and technology inquiry
02-555-7033
info@wezon.com
Leak Detection and Repair System
Leak Detection and Repair System LDAR
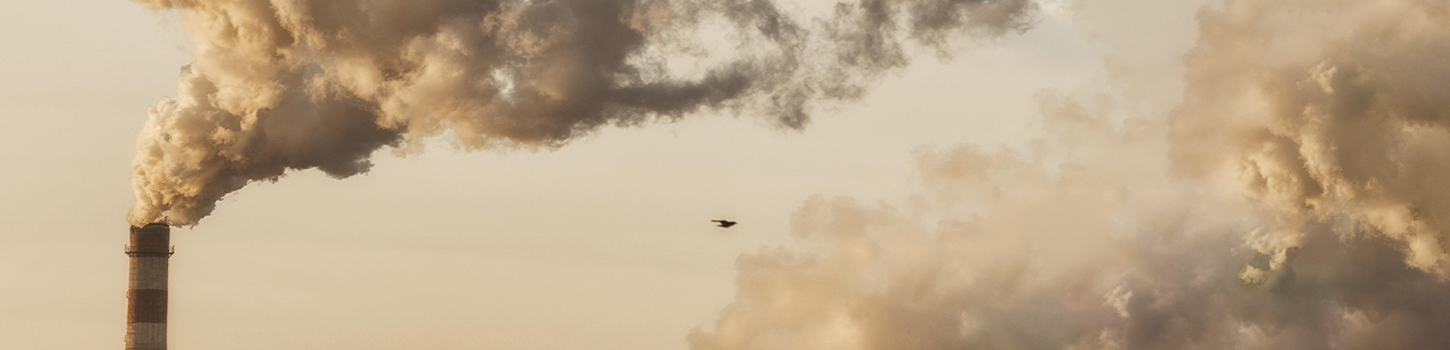

The management system ultimately reduces the discharging of hazardous chemicals through regular leak inspection and repair of fugitive emission
facilities within the workplace.
Importance
As the environmental issues are rising as an international problem, the regulations and laws related to the management of hazardous chemicals,
such as Chemical Substances Control Act, and the management of fugitive emission facilities, such as Air Quality Preservation Act,
are being enhanced by the government and related institutions.
As changes in environmental policies are expected due to internal and external needs, it is necessary to change the business management
environment within the company and establish an effective system to lead such change.
There is also a growing movement within companies to promote the health of employees and an eco-friendly work environment.
System
configuration
diagram
Key functions
Can be connected to various measurement devices |
---|
Can be linked to measuring devices for VOC(volatile organic compounds), carbon monoxide, methanol, etc. : MiniREA 2000, MiniRAE 3000, TVA-1000, V-RAE, etc. Response factor value can be applied to each measuring device |
Leak inspection and repair management |
---|
Automatic setting of annual leak inspection plan Measurement values can be uploaded as excel or on the web Automatic mailing function for leaking equipment Maintenance history search function for leaking equipment |
Calculate emission |
---|
A variety of emission factors can be applied, including emission coefficient correlation equations and leak-based emission factors Integrated emissions can be calculated according to leak inspection method Emissions can be calculated according to various search conditions Response to PRTR emissions reporting is feasible |
Connection with HAPs |
---|
Automatic I/F for HAPs target substances and fugitive emission facilities Fugitive emission facility standard information management Preparation and management of fugitive emission facility operation record Response to operation records and inspection reports of fugitive emission facilities is feasible through leak inspection data I/F |
Expectations
-
Quantitative effects
Reduction of emissions through periodic monitoring/repair of fugitive emission facilities
(09; Emissions survey guidelines, quarterly monitoring)Reduction of raw material loss due to decreased leakage through the management of fugitive emission facilities
Reduce social costs such as civil complaints by establishing an environmental friendly corporate image
Obtain evidence that complies with the Ministry of Environment's guidelines
-
Qualitative effects
Improved working environment and protection of employee health by reducing VOC emissions
Prevention of safety accidents such as fire and explosion(Regular inspection)
Prevent civil complaints by reducing air emissions, such as foul odor
Early response to environmental policies is feasible by securing future system connectivity/scalability
Product and technology inquiry
02-555-7033
info@wezon.com
Hazardous Air Pollutants
Hazardous Air Pollutants management service HAPs
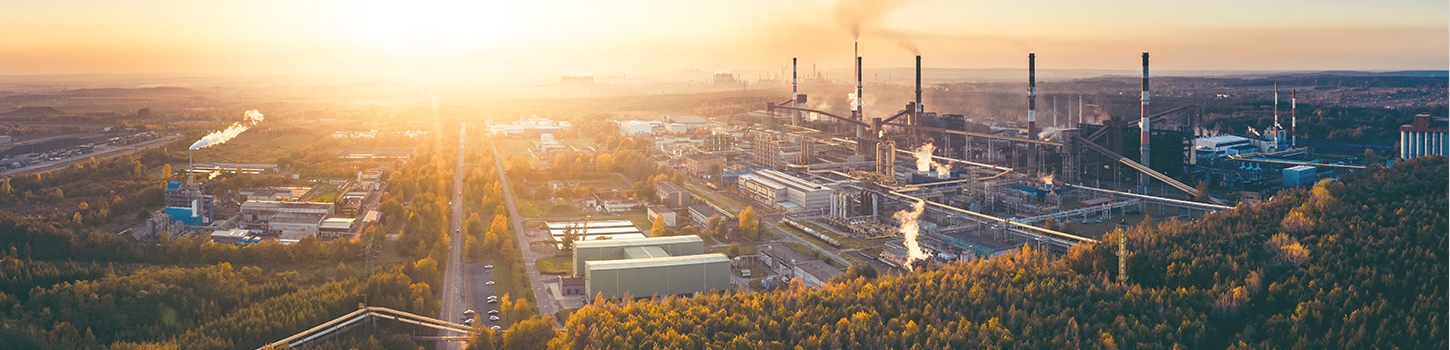

The HAPs fugitive emission facility management system is a system to reduce fugitive emission by managing facilities
and processes that emit hazardous air pollutants(HAPs).
It is very difficult to reduce pollutants discharged into the atmosphere from facilities and processes by managing pollutants centered around existing point
emission sources(chimneys, etc.) without outlets.
Therefore, the Ministry of Environment introduced regulations on monitoring hazardous air pollutants that are discharged from all facilities and processes from raw material
input to product shipment and also facility management standards to reduce fugitive emission.
Importance
Businesses that fall under the scope of industries under Article 38-2 (Businesses subject to reduction of fugitive emission) of the Enforcement
Decree of the Air Quality Preservation Act and have installed and operates substances and emission facilities subject to management in accordance with Annex Table 10-2 of the Enforcement Rules of the same Act must report
and submit initial and annual inspection reports for fugitive emission facilities and receive regular inspections every three years from a regular inspection agency.
Process
Build inventory
Investigate target substances for management
Investigate fugitive emission facilities
Research fugitive facilities
Fugitive facility location information and attach nameplate
Prepare operation record
and measure fugitive emission facilities
Prepare operation record for fugitive emission facilities
Measure fugitive emission facilities
Measure fugitive
emission facilities
Prepare and submit initial and annual inspection reports to the local environmental agency
Ministry of Environment’s regular inspection and maintenance
Korea Environment Corporation’s regular inspection conducted every 3 years
Operation record and leak inspection data related to facility management standards are maintained and stored for 3 years
Services provided
-
01
Regulatory response to HAPs under the Air Quality Conservation Act
Legal response to HAPs by checking compliance with target equipment and facility management standards
Attach location information and nameplate(Tag) by building an inventory of fugitive emission facilities (Reflecting the mandatory standards for identification of fugitive emission facilities implemented from January 1, 2020 due to the revision of subordinate laws of the Air Quality Conservation Act)
-
02
Check whether P&ID(floor plan) matches on-site
Check suitability through marking P&ID and PFD of the substance
Check whether the fugitive emission facility actually exists on site based on inventory prepared based on P&ID
-
03
Consulting for HAPs under the Air Quality Conservation Act
Prepare annual regular report
Application method of facility management standards for emission and fugitive emission facilities
Review facility management standards and ways to reflect revisions for emissions reduction
Check operation record
Product and technology inquiry
02-555-7033
info@wezon.com
Access Control system
Access management system ACCOS
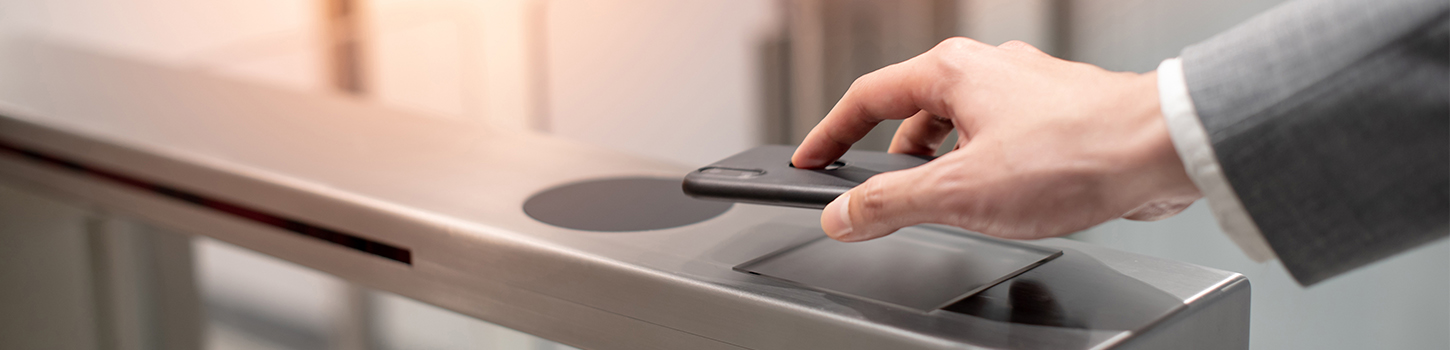

The access management system(ACCOS) counts and manages all matters related to the entry and exit of visitors and vehicles in real time through
computerized management, and improves the convenience of entry and exit of visitors to the factory.
In addition, the company information, workplace location, and information of workers can be managed in real time to determine the work status within the factory,
and the safety of work is improved through systematic computerized management of workers' safety and security training.
Importance
-
01
Control of visitors and vehicles
Personnel entry/exit management and attendance management is required
Management of partners and visitors access areas and work areas
Control and management of visitors and vehicles
-
02
Improve work process
Improvement of unnecessary procedures and shortened waiting times during access of visitors and vehicles are required
Simplified access procedures by creating a database of visitors/vehicles is required
Real time business processing and material identification are required when materials carried in and taken out
-
03
Ensure security and safety
Classification of foreign visitors, executives and employees, and access control according to level is required
Strict compliance with safety/security training for partners and visitors
Access vehicle control management
System
configuration
diagram
Key functions
Basic information management |
---|
Worker information management리 |
Partner information management |
Private vehicle information management |
Business and shipping vehicle information management |
Visitor information management |
Worker information management |
Safety and security education management |
Education management by visitor/company |
Partner education plan and completion status |
Violator and violation company management |
Violator and violation company management |
---|
Visitor reservation management |
Prepare construction access request form |
Personnel access information management |
Vehicle access information management |
Access history management |
Accident and regulation violation history |
Safety education completion history |
License and qualification history력 |
Other access-related history |
Access card management |
---|
Issue/Retrieve electronic card |
Set card access permission |
Set access suspension period |
Set personnel, vehicle information |
Statistics management |
Manpower input report by contract |
Access status by period/company |
Statistics by period/department |
Accident regulation violation report |
Statistics by task/individual |
Statistics by period(Day/Month) |
Expectations
-
Contributes to fostering partners and the safe operation of workers
Analysis of manpower for each construction contract(Man-hour, quality, etc.)
Generate basic report for partner evaluation
Automatic access control for workers who have not completed safety training
Worker violation and accident history management
Access control by level for employees and external visitors
Safety/security training and management for partners, workers, etc.
-
Improve access procedures and import/export work
Improve unnecessary procedures and shorten waiting times during access of visitors and vehicles
Simplified access procedures by creating a database of visitors and vehicles
Establish real-time business processing, location-identified SHE decision-making,
and early response system when import and export materials -
Strengthened safety and protection
Automatic control of unauthorized personnel/vehicles in protected areas
History management and access control for rule violators
Management of access-related data statistics is feasible
-
Improved customer service
Fast factory and office access for Internal and external customers
Simplified access for partners and workers
Strengthened security through separate management of product and personnel access
Number of employees can be managed
Product and technology inquiry
02-555-7033
info@wezon.com
Intelligent Emergency Response System
Emergency Response System iERS
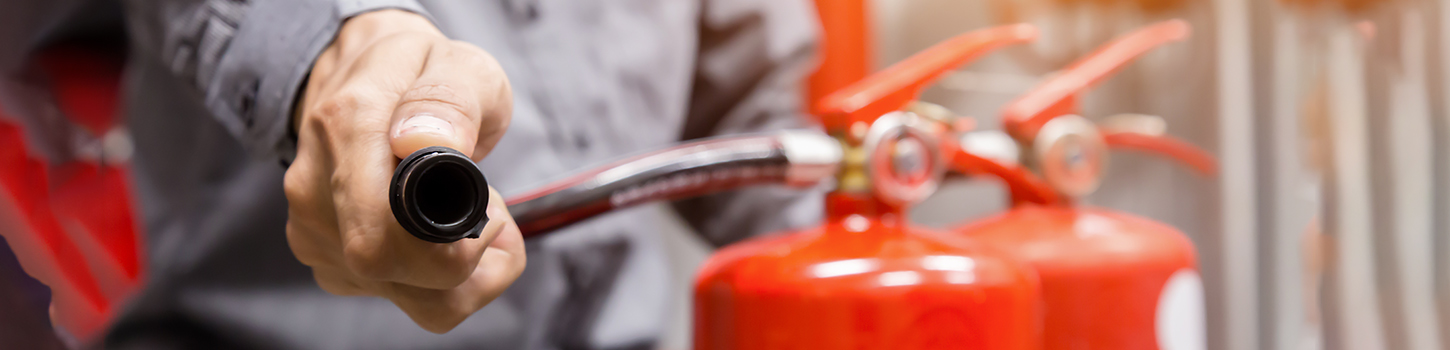

The emergency response infrastructure registers emergency situations that may occur in the process as scenarios in advance,
and enables immediate response by quickly recognizing and disseminating the emergency when it occurs through continuous process monitoring.
It provides a foundation for maximizing productivity through stable factory operation and includes dry training,
which can contribute to enhanced emergency response capabilities through regular training.
Importance
The IT system helps achieve early process normalization through prompt alerts
and hot-line transmission to all plants in the event of an emergency such as a power supply interruption or fire.
System
configuration
diagram
The scope of establishment includes consulting for developing emergency response scenarios along with infrastructure and IT systems.
Expectations
-
Establishment of an emergency response infrastructure
Even during an emergency such as a power outage, communication between control rooms is possible
through a hot-line(using a dedicated network)Communication between the situation room and control room is enabled during the emergency response process
-
Immediate emergency recognition and prompt response
Automatic and immediate recognition in the event of a pre-registered emergency
Prevent the spread of damage by quickly disseminating emergency situations through the hot-line
In the event of an emergency, immediate response is made possible due to predetermined response procedure
Achieve early normalization of the process through sufficient communication between the situation room
and control room -
Systematic management of simulation training
Strengthened emergency response posture through regular simulation training
Systematic management of simulation training plan and results
Continuous improvement of emergency response scenarios through training process
Contributes to the reduction of emergency situations by enhancing careful driving
-
Computerization of DCS alarm management
Automatic recognition of emergency situations through DCS alarm
Improved sharing and usability of alarm results
Product and technology inquiry
02-555-7033
info@wezon.com